|
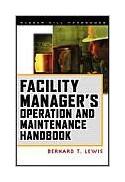
FACILITY MANAGER'S OPERATION AND MAINTENANCE HANDBOOK
LEWIS B. wydawnictwo: MCGRAW-HILL , rok wydania 1999, wydanie I cena netto: 555.00 Twoja cena 527,25 zł + 5% vat - dodaj do koszyka Provides a uniquely
integrated and coordinated approach to operating and maintaining facilities that maximizes
their performance at the least cost. Offers a complete picture of facility operations and
maintenance including staffing, computer controls, technical improvements, maintenance
procedures, outsourcing, and repairs. Enables facility managers and engineers to
anticipate and correct minor problems before they turn into expensive disasters. Reflects
the practical knowledge and experience of 21 specialists in facility operations and
maintenance.
Here are cutting-edge techniques that will boost the productivity and slash the costs of
your facility department
Let 21 top specialists show you how to maximize the operation and maintenance capabilities
of any facility or plant. This practical handbook takes you through each step in the
planning, design, and execution of maintenance and operation procedures for structures,
equipment, and systems. It features special emphasis on emergency and energy equipment
used in facilities and explores all essential support functions and duties. The most
comprehensive resource of its kind, this handbook provides you with a complete picture of
facility operation and maintenance from technical checklists to cost control to computer
applications!
Table of Contents
Foreword
Preface
Contributors
Part I: Organizing for Maintenance Operations
CHAPTER 1-Program Organizational Structure
1.1 Responsibilities and Authority
1.2 The Facility Manager
1.3 Facility Planning
1.4 Facility Engineering and Design
1.4.1 Modification or Major Repairs
1.5 Engineering Support to the Maintenance and Operations Functions
1.5.1 Specialized Technical Services
1.5.2 Cost Reduction
1.6 Construction of Facilities and Installation of Equipment and Systems
1.6.1 Personnel in Facility Organizations-Single Project Worker-Hour Limit
1.7 Maintenance of Facilities and Systems Equipment
1.8 Preventive Maintenance
1.9 Routine Maintenance
1.10 Major Repairs
1.11 Alterations and Improvements
1.12 Housekeeping
1.13 Principles of Organization
1.13.1 Definition and Scope
1.14 Facilities Management Defined
1.14.1 Facility Management Functions
1.14.2 Organizational Prerequisites
1.15 Analyzing the Needs
1.16 Establishing Goals and Objectives
1.17 Administering the Organization
1.18 Organization vs. People
1.19 Using Titles
1.20 Performance Measurement
1.21 Organizing Considerations for Outsourcing Functions
CHAPTER 2-Program Operations
2.1 Designing the Maintenance Management Information System
2.1.1 What Kind of Information Do You Need?
2.1.2 Common Information Needs
2.1.3 Special Information Needs
2.1.4 Hardware and Software Requirements
2.2 Functions of the System
2.2.1 Maintenance Planning and Scheduling
2.2.2 Corrective Maintenance
2.2.3 "House Calls"
2.2.4 Projects
2.2.5 Parts Availability
2.2.6 Information System Integration
2.2.7 Use of Preventive and Predictive Information
2.2.8 Warranties Information
2.2.9 Production and Financial Support
2.2.10 Personnel Data
2.2.11 Quality Control and Quality Assurance Data
2.3 Annual Maintenance Operational Report
2.3.1 Elements of a Successful System
2.3.2 Maintenance History vs. Machinery History
2.3.3 Production and Financial Reporting
2.3.4 Quality Management Impact
2.3.5 Maintenance "Outplanning"
2.4 Maintenance Management Manual
2.4.1 Scope of the Manual
2.4.2 Maintenance Objective
2.4.3 Lines of Authority
2.4.4 Task Responsibility
2.4.5 Corrective Action
2.4.6 Regular Review of Feedback
2.4.7 Document Control
2.4.8 Regular Review of Entire System
2.5 Other Considerations
Part II: Facility Operations and Maintenance Plans
CHAPTER 3-Operations Plans
3.1 Management Operational Plan
3.1.1 Work Control Methods and Procedures
3.1.2 Work Control Center
3.1.3 Service Orders (SO)
3.1.4 Work Orders (WO)
3.1.5 Standing Operating Orders (SOO)
3.1.6 Preventive Maintenance (PM)
3.1.7 Work Priority System
3.1.8 Emergency Priority
3.1.9 Urgent Priority
3.1.10 Routine Priority
3.1.11 Work Approval
3.1.12 Planning
3.1.13 Scheduling
3.1.14 Execution of Work
3.1.15 Checked and Inspected
3.1.16 Closed and Cost Accounted
3.1.17 Results Recorded, Analyzed, and Measured
3.1.18 Feedback
3.2 Building Operational Plan
3.2.1 Scheduling Work
3.2.2 Shutdowns and Startups
3.2.3 Emergency Situations
3.2.4 Trouble Diagnosis and Coordination
3.2.5 Coordination with Third Parties
3.2.6 Benchmarking
3.2.7 Statistical Process Control
3.3 Comprehensive Facility Operational Plans
3.3.1 Emergency Response Plan
3.3.2 Hazardous Materials Plan
3.3.3 Refrigerant Management
3.3.4 Safety Plans
3.3.5 Fire Protection Plans
3.3.6 Labor Unrest
3.4 Facility Occupant Support Plan
3.4.1 Improving Perceptions
3.4.2 Determining Wants
3.4.3 Provide Feedback
3.5 Quality Control Plan
3.5.1 Specific QCP Objectives
3.5.2 Inspection System
3.5.3 Inspections by FD Personnel
3.5.4 Identifying and Tracking Substandard Performance
3.5.5 Correcting Deficiencies
3.5.6 Total Quality Management (TQM) Program Specifically for O&M Procedures
3.5.7 Tenant Relations Program
3.5.8 Tenant Visit Report
3.6 Summary
CHAPTER 4-Maintenance Plans
4.1 Equipment, Systems, and Structure Building Tours
4.1.1 Introduction
4.1.2 Purpose
4.1.3 Implementation
4.1.4 Scheduling
4.1.5 Equipment and System Logs
4.1.6 Technology
4.1.7 Staffing
4.1.8 Documentation
4.1.9 Summary
4.2 Engineered Performance Standards (EPS) Usage Plan
4.2.1 Basis for All Types of Labor Time Standards (EPS)
4.2.2 Computerization
4.2.3 Why Have Labor Time Standards?
4.2.4 Types of EPS
4.2.5 Estimate
4.2.6 Historical Work Standards
4.2.7 Direct Observed Standards
4.2.8 Published Engineered Performance Standards
4.2.9 Engineered Performance Standards
4.2.10 Management Manuals
4.2.11 Trades Manuals
4.2.12 General Services Administration: Public Buildings, Maintenance Guides and Time
Standards
4.2.13 R.S. Means Maintenance Standards
4.2.14 How to Use Standards, a Step-by-Step Guide
CHAPTER 5-Preventive Maintenance (PM) Plan
5.1 PM Procedures
5.1.1 Dollars and Cents
5.2 Automated Program-Software
5.2.1 Getting Started with CMMS
5.2.2 Flexibility and User-Friendliness
5.2.3 Generic CMMS Function
5.2.4 Implementing a CMMS
5.3 Maintenance File Cards
5.4 Equipment History Files
5.5 Verifying Facility Inventory
5.6 Labeling Facility Equipment
5.7 Annual PM Schedule
5.8 Setting Special Schedules
5.9 Opening or Dismantling Equipment
5.10 Computerized Records and Reporting
CHAPTER 6-Predictive Maintenance Plan
6.1 Benefits of Predictive Maintenance
6.2 Predictive Maintenance Technologies
6.2.1 Vibration Monitoring
6.2.2 Infrared (IR) Thermography
6.2.3 Oil Analysis
6.2.4 Ultrasound
6.2.5 Integration
6.2.6 Expert Systems
6.3 Predictive Process
6.3.1 Program Startup
6.3.2 Measure Program Effectiveness
6.3.3 review and Revise Program
CHAPTER 7-Indoor Air Quality (IAQ) Plan
7.1 IAQ and the Contemporary Facility Manager
7.1.1 Indoor Pollutants
7.1.2 Sick Building Syndrome
7.1.3 Causes and Considerations
7.1.4 Facility Managers Go Proactive
7.2 The Proactive Facility Inspection and Sampling Techniques
7.2.1 Objectives
7.2.2 Scope of Proactive Facility Inspection
7.2.3 Analysis of Building Data
7.2.4 HVAC Inspection
7.2.5 Air Quality Tests
7.2.6 Outdoor Air
7.2.7 Water Quality Testing (Associated with HVAC Systems)
7.2.8 Drinking Water Sampling and Analysis
7.2.9 Other Tests
7.2.10 Facility Inspection Reports
7.2.11 Facility Reinspections
7.3 Avoidance Procedures
7.3.1 Preventive Operations, Maintenance, and Policy
7.3.2 Designing Healthy Buildings
7.3.3 Managing IAQ Risk within Leases
CHAPTER 8-Technical Improvements Plan
8.1 Total Quality Management (TQM) Program
8.1.1 TQM-What It Is
8.1.2 TQM-What It Is Not
8.1.3 Rewards to Be Reaped
8.1.4 How Does TQM Work?
8.1.5 Summary: What to Do to Keep TQM on Track
8.2 Walue Improvement Program
8.2.1 Validation of Value
8.2.2 Value Engineering
8.2.3 Synergistic Opportunities
8.2.4 Successful Value Engineering
8.2.5 Increase Value
8.2.6 Value Perceptions
8.2.7 Why Does Poor Value Occur?
8.2.8 Value Engineering Process
8.3 Energy Management Program
8.3.1 Overview
8.3.2 Mechanical Systems
8.3.3 Control Systems
8.3.4 Energy Management Programs
8.3.5 Chiller Plant
8.3.6 Hot Water Reset
8.3.7 Lighting Controls
8.3.8 Conclusions
Part III: Equipment and Systems Operations and Maintenance Procedures
CHAPTER 9-Equipment and Systems Operations Procedures
9.1 Equipment Inventory
9.1.1 Conditions Assessment
9.1.2 Design Assessment
9.2 Operational Requirements
9.2.1 Equipment Startup and Shutdown
9.2.2 Operational Checks
9.2.3 Lighting
9.2.4 Relamping
9.2.5 Energy Conservation
9.2.6 Use of Demand Control Ventilation
9.3 Facility Management Tools
9.3.1 Energy Management Control System (EMCS)Operations
9.3.2 Emergency and Extended FMS Operations
9.3.3 FMS Service Program
9.3.4 FMS Operating Personnel Requirements
9.3.5 Remote Control Operating Requirements
CHAPTER 10-Mechanical Equipment and Systems Maintenance Procedures
10.1 Preventive Maintenance Program
10.1.1 Purpose of PM
10.1.2 Practice of PM
10.1.3 Size of PM Activity
10.1.4 Definition of PM
10.1.5 Efficiency of PM
10.1.6 Engineering Input
10.1.7 Analysis of Maintenance Needs
10.1.8 Proper Use of Equipment
10.1.9 Basic Controls
10.1.10 Field Inspection Procedures
10.1.11 Feedback, Properly Supplied and Utilized
10.1.12 Labor Standards Applied to PM
10.1.13 How PM Relates to Other Routine Maintenance
10.1.14 Additional PM Program Techniques
10.2 Facilities Inspection and Maintenance Program
10.2.1 Computers
10.2.2 Reduction in Overall Maintenance Effort
10.2.3 Doing Only What Needs to Be Done
10.2.4 Plan Some Maintenance and Fire Fight the Remainder
10.2.5 Facilities Inspection and Maintenance Program Specifics
10.3 Equipment and Systems Maintenance and Repair Procedures
1069 pages
Po otrzymaniu zamówienia poinformujemy, czy wybrany tytuł polskojęzyczny lub
anglojęzyczny jest aktualnie na półce księgarni.
|